Die Entwicklung der Schweißtechnik auf der Volkswerft Stralsund 1990 - 2020
​
1989 kam es in der damaligen DDR zur politischen Wende. Dies hatte dann natürlich einen großen Einfluss auf die Entwicklung der Schweißtechnik. Durch die Öffnung des Marktes standen vielfältige Möglichkeiten zu Verfügung um die Effizienz der Schweißtechnik zu steigern. Die Acetyleneigenerzeugung wurde auf Trailerversorgung umgestellt. Es wurden umfangreiche Erprobungen und Schweißversuche mit neuer Schweißgerätetechnik, Schweißzusatzwerksoffen sowie Hilfsstoffen durchgeführt.
​
Etabliert wurde zum Beispiel:
-
das Schweißen mit Fülldraht unter Schutzgas ( COâ‚‚, Mischgas)
-
das Einseitenschweißen auf keramischer Badsicherung
-
das Schweißen von CuNiFe-Rohren
-
das Zinkschweißlöten von verzinkten Rohren
-
Einsatz der Bolzenschweißtechnik zum Klammern und Ausrichten von schiffbaulichen Schweißstößen, sowie zum Anbringen von Halterungselementen in der Ausrüstung
-
schrittweiser Ersatz stromintensiver Stromquellen (Umformer) durch moderne Invertertechnik
​
Der Bau der 3 Hurtigroutenschiffe stellte mit dem Einsatz von Dünnblechkonstruktionen, Alu-Aufbauten und sprengplattiertem Material eine Herausforderung für die Schweißtechnik dar.
​​​
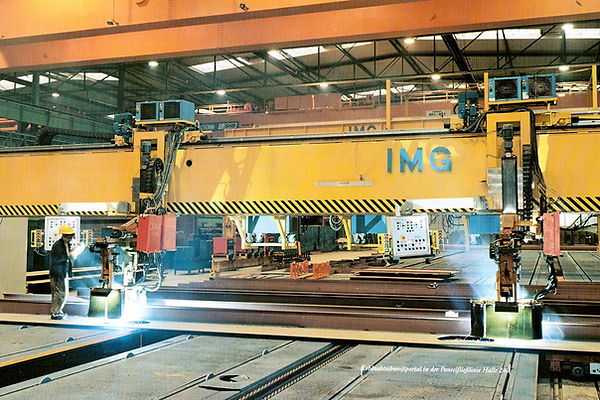
Kehlnaht-Schweißportal in der Panelfließlinie Halle 240
1994 begann die Modernisierung der Volkswerft hin zu einer Kompaktwerft um die Wettbewerbsfähigkeit der Volkswerft zu sichern. Alles geschah bei laufender Produktion. Für die Schweißtechnik bedeutete das:
-
Errichtung einer modernen UP-Einseitenschweißanlage mit 3-Schweißdrähten
-
Bau einer teilautomatischen Kehlnahtschweißanlage zum Schutzgasschweißen von Schiffbauprofilen
-
Schweißrobotereinsatz beim Schweißen von Kehlnähten im Doppelbodenbau und in der Mikropaneellinie
-
Einsatz eines Portals zum Aufsetzen und Heften von Profilen
-
Plattenzuschnitt erfolgt mit kombinierter Autogen/Plasmaunterwasser-Schneidanlage
-
Modernisiert wurde auch die gesamte Gasversorgung der Werft, die Gase Argon, Sauerstoff, Kohlendioxid, Acetylen und Mischgas gelangen nun über Ringleitungen zum Verbraucher
-
Installation einer zentralen Schweißrauchabsaugung
​
Neben diesen Großinvestitionen ging die Kleinrationalisierung in der Schweißtechnik natürlich weiter. Es wurden Schweißversuchen mit schienengeführten Schweißsystemen (KAT, BUG-O ) an Volumenstößen durchgeführt. Der Einsatz von Kleintraktoren für die Kehlnahtschweißung wuchs stetig. Beim UP-Schweißen wurden ebenfalls Traktoren für das Schweißen von Stumpfnähten eingesetzt. Im Gegensatz zum Einseitenschweißen erfolgte das Schweißen beidseitig, d.h. das Bauteil musste gedreht werden um die Naht fertigzustellen. Für das Schweißen von gebauten Profilen (T-Profil) wurde ein kleines UP-Portal auf Basis der Schlepparmtechnik installiert.
Durch die vielfältige Produktpalette an Schiffstypen und den Einsatz immer neuer Stahlsorten mussten umfangreiche Schweißverfahrensprüfungen abgelegt werden, um den Nachweis der Schweißeignung für die Werft zu erbringen. Hierbei spielten die Vorschriften der Schiffsklassifikationsgesellschaften ( GL, LR, BV, DNV usw.) natürlich eine große Rolle. Auch die Schweißer/Schiffbauer/Schlosser mussten sich diesen Herausforderungen stellen. In der betriebseigenen Ausbildungsstätte wurden ständig Schulungen und Abnahmen von Schweißer-Prüfungen durchgeführt. Die Änderungen im Regelwerk (DIN, EN, ISO) für das Ablegen von Schweißer-Prüfungen verlangten auch von den Ausbildern immer wieder hohen Einsatz.
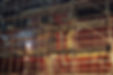
​​
Der Bau von Offshorekomponenten , wie Spudcan, ein Fundament für die Verankerung von Bohrtürmen (Jackets), DOLWIN III, ein Jacket für die Aufnahme einer Konverterstation verlangten hohe Qualitätsanforderungen von den Schweißern , d.h. das beim Schweißen von Wandstärken bis 90 mm eine immense Konzentration gefordert war, um Schweißnahtfehler zu vermeiden. Das Ergebnis der Schweißnahtprüfungen bestätigte die hervorragende Qualitätsarbeit der Schweißer. Neben einem kleinen Anteil an der UP-Schweißung wurden alle anderen Schweißnähte mit dem Schutzgasschweißen (MSG) ausgeführt.
​
Abhängig von den jeweiligen Bauprojekten entwickelte sich die mechanisierte und teilautomatische Schweißung immer weiter. Der Anteil der E-Hand-Schweißung spielte eigentlich nur noch eine Rolle bei Heftarbeiten im Bereich der Ausrüstung. Basierend auf den Verbrauch von Schweißzusatzwerkstoffen kann man den Anteil wie folgt definieren: 5% E-Hand, 10% UP, 85% MSG
​
Nach vielen Eigentümerwechseln übernahm 2016 der Genting-Konzern die Werft, die bis dahin zur Nordic Yards Gruppe gehörte, neben der Werft in Wismar und Warnemünde. Diese drei Werften firmierten unter dem Namen MV-Werften. Um die Produktionsziele zu erreichen, Bau von Luxuslinern, wurde vom Genting-Konzern ein umfangreiches Investitionsprogramm gestartet und realisiert.
​
Die bisherige Technik die seit 20 Jahren im Einsatz war genügte nicht mehr den Anforderungen. Erneuert wurde die gesamte Paneelfertigung ( UP- Einseitenschweißanlage, Kehlnahtschweißportal), sowie die Mikropaneelfertigung. Die manuelle Schweißung war auf dem Stand der Technik und wurde nur punktuell erneuert
​
In der Werft in Stralsund wurde das Expeditionschiff „Endeavour“ gebaut und zu guter Letzt auch noch fertiggestellt. Mit dem Beginn der Coronakrise kam auch der Genting-Konzern in eine finanzielle Schieflage. Es kam 2020 zum Baustopp. Durch finanzielle Unterstützung von Bund und Land konnte weitergebaut werden bis im Januar 2022 Insolvenz für die MV-Werften angemeldet wurde.
​
Damit endete eine Epoche erfolgreichem Schiffbau auf der „Volkswerft“ in Stralsund